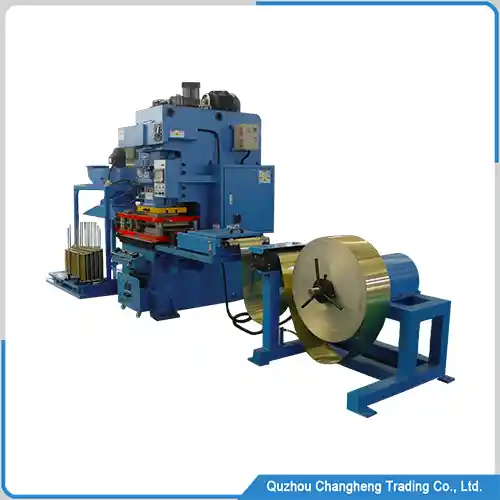
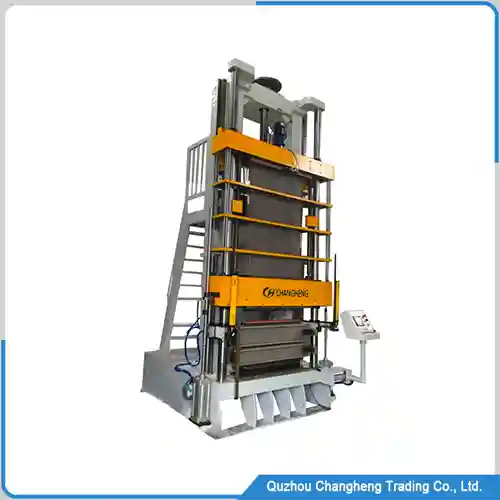
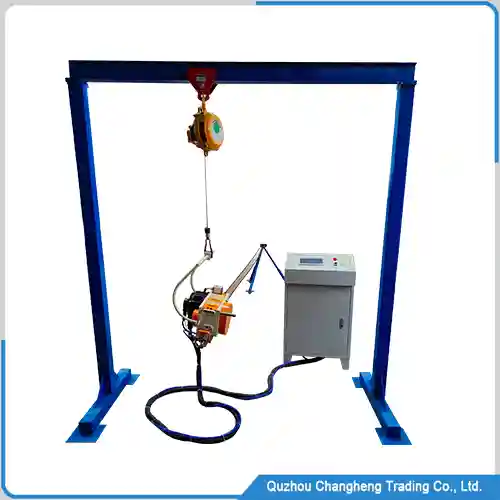
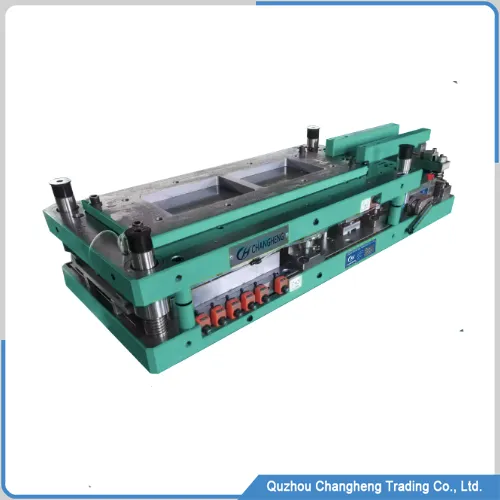
Product Description
This fin die is used to produce heat exchanger aluminum fins. It comprises multiple independent pressing mold units to form a highly automated production stamping mold.
This mold ensures consistency in the shape and size of each part during high-speed production while maintaining a good tolerance range.
The mold’s interior is modular, and key components can be independently replaced to check its service life.
Fin die application field
This mold is fully automated and can manufacture cooling fins for raw metal materials, such as copper, aluminum, iron, stainless steel, hydrophilic aluminum foil, etc. Therefore, its application is very extensive.
Below are a few examples of its usage areas
A tube and shell-type heat exchanger, typically with a circular fin shape, is installed inside the shell
One of the most commonly used products is household air conditioning, where almost every condenser relies on fin molds
There is a type of car radiator that uses a tube and fin structure, which requires fin dies to produce the entire core
Due to the flexible arrangement of geometric structures in this mold, many large industrial heat exchangers use this fin mold
The heat exchanger for home heating uses copper fins to increase heat transfer efficiency, which requires fin mold production
Fin Die Raw Materials
Part name | Raw materials |
Louver parts | SKH51 |
Mold Spring | 50CrVA |
Punch needle | SKH51 |
Small mold plate | Cr12MoV |
big mold plate | EN C45 |
Mold type and technical parameters
- Hole diameter: (3/8’’) 9.52mm
- Collar height: 2.5-5mm
- Continuous production: Yes
- Geometry size: 25.4*23mm
- Hole Quantity: 12 rows
- Overall dimension: 1050*540*240mm
- Step: 1-row hole or 2-row hole
- Edge cutting: wave, straight line
- Hole size: 12.7mm
- Collar height: 3.5-7mm
- Continuous production: Yes
- Geometry size: 31.75*27.5mm
- Hole Quantity: 12 rows
- Overall dimension: 1250*550*320mm
- Step: 1-row hole
- Edge cutting: wave, straight line
- Hole size: 15.88mm
- Product name: Fin die
- Collar height: 2.5-5mm
- Continuous production: Yes
- Geometry size: 38.1*33mm
- Hole Quantity: 8 rows
- Overall dimension: 1450*560*340mm
- Step: 1-row hole
- Edge cutting: wave, straight line
- Hole size: 16.3mm
- Collar height: 3.5-8mm
- Continuous production: Yes
- Geometry size: 50*50mm
- Hole Quantity: 6 rows
- Overall dimension: 1450*560*320mm
- Step: 1-row hole
- Edge cutting: wave, straight line
Fin press die advantages
1. Diversified geometric layout, one stamping die can produce products of various sizes
2. Workers do not need to be supervised during production, and the fin die can be fully automated.
3. The independent design of key components allows for low-cost replacement and extends the lifespan of molds.
4. Allow users to quickly replace molds and install different fin molds on a stamping machine.
5. This mold has an automatic feeding device for fast and high-precision production.
Heat exchanger fin die manufacturer factory video
Other stamping molds
Fin progressive die of heat exchanger
Mold Overview 1. This fin Progressive die is suitable for automobile radiators, household air conditioners, central air conditioners, dehumidifiers, etc. 2. It is suitable for aluminum foil with different states and thicknesses at home and…
Condenser fin mold and Progressive die
Product Introduction The condenser fin mold is a tool for continuous high-speed production. It is a fully auto progressive mold tool that combines multiple molds with different functions. This mold is the main production tool…
Plastic Injection mold of radiator tank
Mold Overview This plastic injection mold for car radiators has a hot runner control and water cooling device inside. It can be installed on any brand of horizontal injection machine for use, We specialize in…
Q & A
A: The packaging of this mold is a wooden crate
A: Our die delivery time is 50-62 days
A: Our molds are suitable for more than 90% of stamping machines, You can contact our engineer and provide pictures of your stamping machine
A: We can customize all dimensions of the mold according to the customer’s requirements