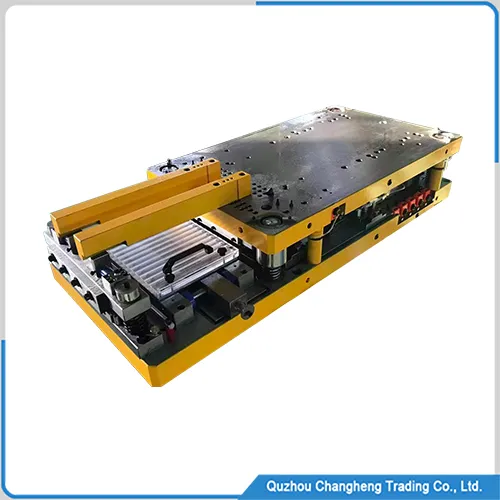
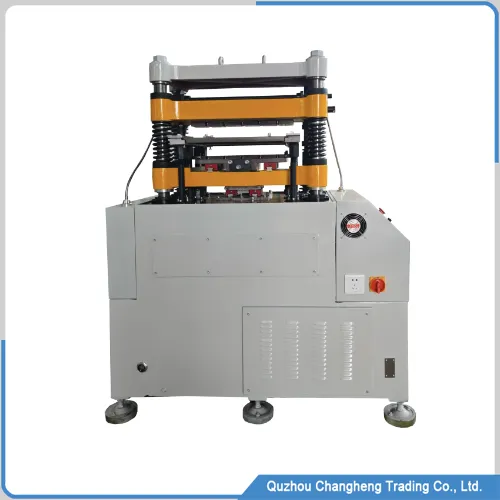
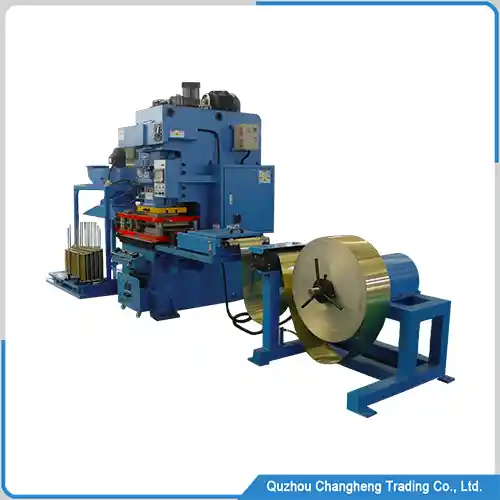
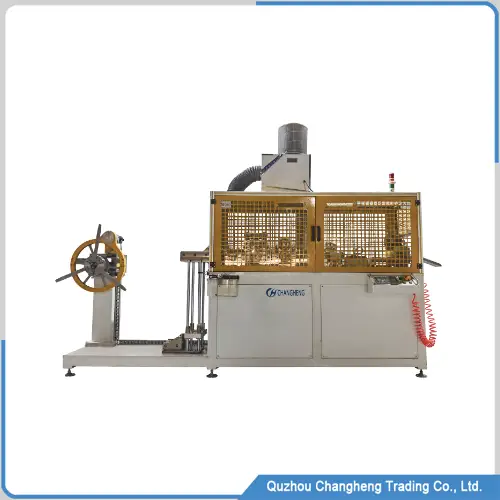
Tooling Overview
Fin die tooling is a type of mold used in the manufacturing process of heat exchangers, specifically designed for stamping metal foil materials to form fins with specific shapes and sizes.
These fins enhance the heat exchange capacity of the heat exchanger as they increase the contact area between the fluid and the metal surface.
Fin die parts are usually made of high-strength and wear-resistant materials, such as hardened steel or carbon steel,
to withstand the high pressure of stamping machines and long-term production operations.
Fin die tooling design
The design of the fin model must take into account the following factors:
1, Material characteristics:
The mold material must have sufficient hardness and toughness to resist the stress and wear generated during stamping.
2, Stamping accuracy:
The mold must be precise to ensure that the punching fins have consistent dimensions and smooth edges and meet design requirements.
3, Production efficiency:
Fin die design should support high-speed production to improve overall production efficiency and reduce manufacturing costs per unit product.
4, Maintenance and replacement:
The fin mold should be easy to maintain and replace components, and unique parts need to be design separately for quick replacement in the future
5, Adaptability:
The mold may need to adapt to different thicknesses of sheets or fin designs of different shapes to provide production flexibility.
Fin die tooling details
ITEM | DATA |
Material: | SKH51 |
Hardness: | 58-62 |
Design type: | Quick installation |
Part size | customized |
Tolerance: | 0.001-0.01mm |
Processing method: | high-precision |
In the manufacturing process, the fin mold uses a stamping machine to press the metal sheet into the desired shape, and then the fin is made through cutting, bending, or other subsequent processing steps.
The quality of fin mold components directly affects the quality of heat exchanger fins, which in turn affects the performance and efficiency of the heat exchanger
Therefore, the design and manufacturing of fin molds require high precision and professionalism.
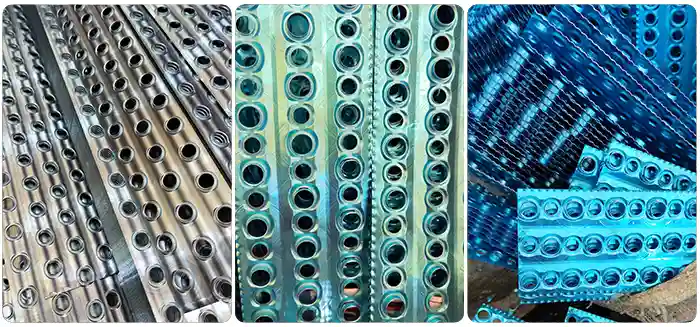