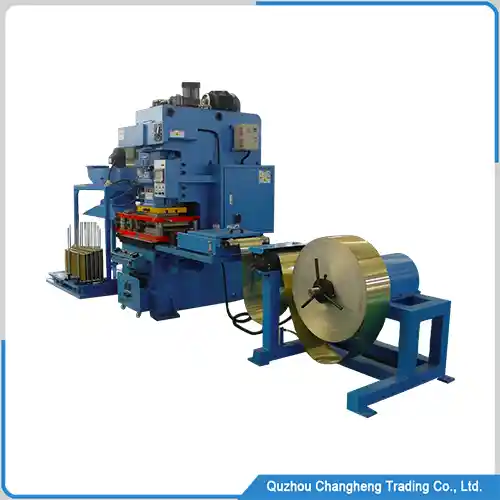
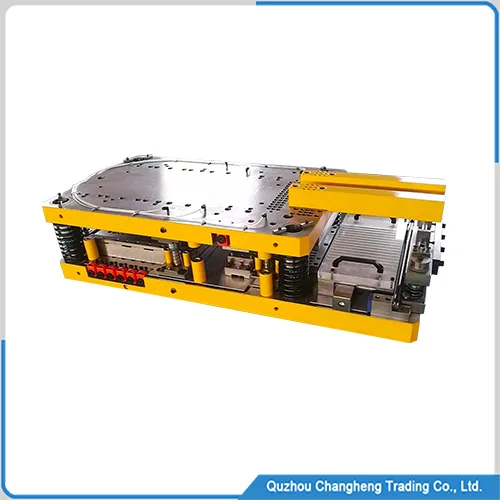
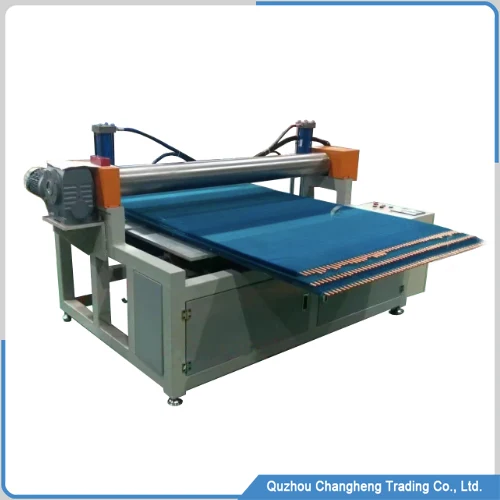
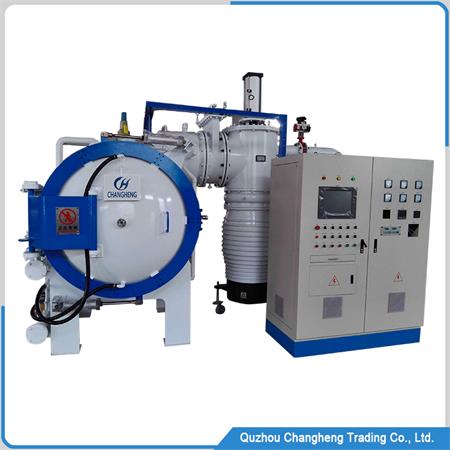
Product Description
This Fin press line is C-type stamping equipment for high-speed production of heat exchanger fin parts. It comprises a material feeder, stamping machine and mold, fin storage device, and other parts.
This device’s pneumatic clutch flywheel controls it to achieve high-speed production and smooth operation. Its fastest production speed can reach 280 punches per minute.
At the same time, the high-speed fin press has an automated production mode. In this mode, engineers set the fins’ length, width, and quantity. When the production requirements are met, the press automatically stops.
Technical Parameter
ITEM | CH-C45 | CH-C63 |
Capacity | 450KN | 630KN |
Stroke Speed | 120-200 S.P.M | 120-200 S.P.M |
Max fin Die | 270mm | 290mm |
Machine Table Size | 580*850mm 660*850mm | 580*850mm 660*850mm |
Bottom Size | 300*400mm | 360*500mm |
Overall size | 700*250*265cm | 720*258*295cm |
Weight | 6.5T | 7.8T |
total Power | 5.5kw | 7.5kw |
foil Coil Width | 310mm | 350mm |
Fin press line features
Efficient and energy-saving
The high-speed punching machine adopts an efficient pneumatic driving device, which allows for high-speed, stable operation and reduced energy consumption.
High precision
The high-speed fin press line machine has high-precision control and automation systems. An automatic lubrication device in the middle of the slider reduces wear between parts and achieves high-precision output.
Energy conservation and environmental protection
The high-speed punching machine adopts the latest environmental protection technology and design. It does not maliciously consume energy or generate waste, making it energy saving and environmentally friendly.
Intelligent
The high speed fin press line machine adopts an intelligent monitoring system and fault alarm mechanism, which can detect and handle faults on time, reducing down time and maintenance costs.
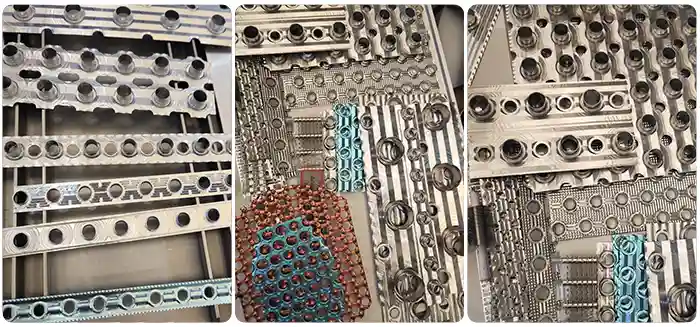
Fin press line advanced function
- The stamping machine has a drawer at the bottom, where waste generated during production is automatically stored to maintain cleanliness around the machine.
- This fin press machine has multiple lubricating oil tanks specially designed to add lubricating oil to the machine’s multiple positions and molds by pressing the oil pipe’s handle.
- We have reserved multiple solenoid valves for the fin punching machine, which mainly controls compressed air output to the mold and fin storage equipment.
- The pressure gauge, flywheel pointer, and fin punch press slider size are all displayed digitally, making it easy for engineers to view these essential production parameters.
Fin press line success stories video
Installation precautions of the fin press line
1. This machine may experience vibrations during average production, so it can only be installation on the factory’s first floor.
2. If possible, please reinforce the ground where the machine is installation with concrete, with an area of approximately 2 * 2 meters and a depth of roughly 0.5-1 meters.
The stamping machine’s long-term rapid vibration may cause irreversible damage to the soft ground.
3. This fin press line requires a usage area of 2 * 5 meters, and space needs to be reserved on both sides according to the raw materials.
4. When the machine is working, usually place a warning sign at the position of the stamping machine to allow non professional workers to approach the machine.
5. The stamping machine has lubricating oil tanks at multiple locations, and it takes about 2-3 weeks to press the handle to add lubricating oil.
Fin press line applications field
- Electronics industry: Cooling devices for production equipment
- Household use: air conditioning condenser, home heating,
- Household appliances: water heater, portable cooling fan
- Automotive industry: engine radiator, air conditioning condenser, heater
- Aviation: Oxygen production equipment
- Industrial field: large scale heat exchanger equipment,
Installation of fin molds
requires a special forklift to lift or lower it when installing the mold. When replacing molds, we need to operate under the premise of ensuring safety, and all the power of the stamping machine should be turned off.
The top of the mold has a quick installation screw hole design, allowing engineers to install the mold in a short time.
During manual debugging of the mold, the bottom plate of the mold needs to be connected to compressed air, and the positioning pin of the mold will rise. The aluminum foil is manually moved through this positioning device until the hole of the aluminum foil contacts the automatic feeding device.
Q & A
A: This machine can install a mold width of 550 – 600mm. Contact our engineers for more details on the machine.
A: This Fin press line includes a coil uncoiling machine, oil tank, main stamping machine, and vacuum receiving machine.
A: Usually, it requires 25 liters of 46 # engine oil.