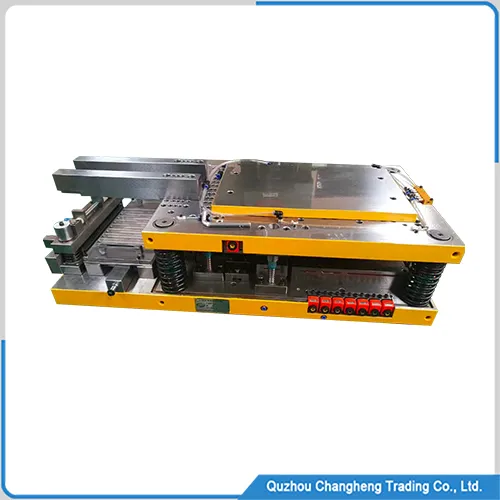
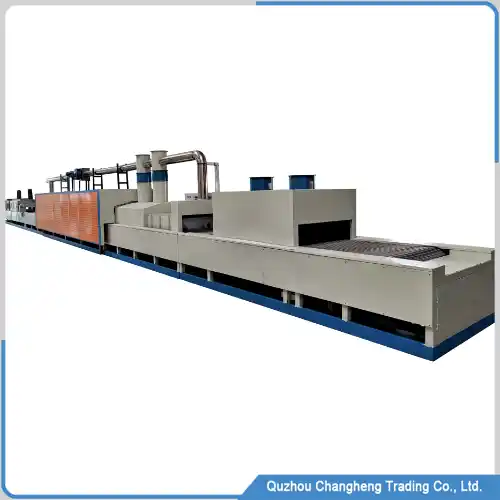
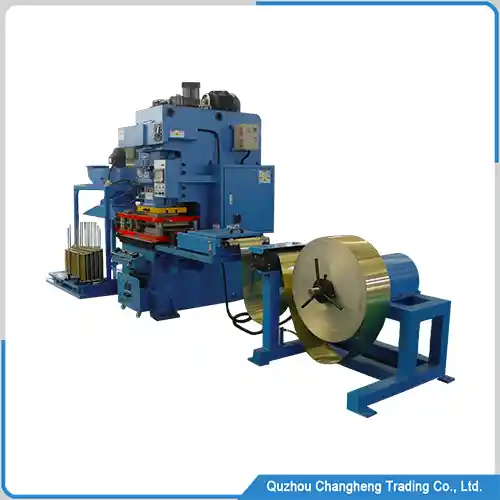
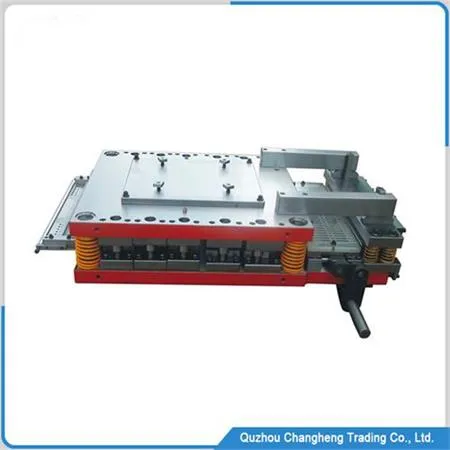
Fin Die Overview
Fin stamping die play a crucial role in the HVAC fin stamping industry. They are not only a high-performance innovative tool, but also renowned for their excellent tolerance accuracy in the industry.
The design of these Fin dies allows for adjustable stretching height when stamping thinner metal materials, which means that various fins of different heights can be produced during the production process to meet the various needs of different customers
In terms of functionality, these fin stamping tools are very flexible and can produce various types of fin patterns.
Whether it is traditional linear fins, more complex offset or serrated fins, or even unique designs such as herringbone or wave shapes, these tools are capable of handling them.
The diversity of this design makes the Fin stamping die perform well in meeting the customized needs of fins in different radiators and HVAC systems.
Fin stamping die data
ITEM | DATA |
Heat treatment hardness | HRC 62-64 |
Place of Origin | Germany |
Hole Diameter | Follow the design |
Material Thickness | 0.05-0.5mm |
Foil raw materials | iron aluminum copper Stainless steel |
rows | 4-20rows optional |
Column spacing | Follow the design |
Line spacing | Follow the design |
Fin stamping die Basic structure
1, Upper and lower mold seats:
This is the basic support structure of the progressive mold, used for installing and fixing other components of the mold.
2, Feeding mechanism:
This is a mechanical structural design that does not require maintenance and upkeep
3, Stamping die cavity:
used to achieve the cutting, forming, punching, and other processing processes of the strip.
4, Cutting device:
This Fin stamping die device usually has a horizontally moving cylinder,
5, Guide pillar and guide sleeve:
Ensure that the relative positions of the upper and lower molds are accurate and error-free during the closing and opening process, ensuring the normal operation of the mold.
6, Positioning device:
used to ensure the correct position of materials during the feeding process and prevent waste caused by misalignment.
The structural design of fin dies needs to consider various factors such as production efficiency, processing accuracy, mold life, and manufacturing cost to ensure their reliability and economy in the production process.