Product Introduction
The industrial vacuum furnace is a professional equipment in the heat treatment industry. The furnace chamber is a closed space that utilizes the characteristics of the vacuum environment to create an oxygen-free environment. Metal parts are treated with hardening, brazing, tempering, and other processes in a vacuum oxygen-free environment.
A vacuum furnace usually consists of a furnace body, a water cooling device, a control system, a vacuum system, a heating device, a transformer, and other parts. Vacuum furnaces with different production processes may have some differences in details.
The current vacuum furnace control system uses PLC as the command execution processor. Users can program logic commands to set different product heat treatment processes. The built-in storage can save these command programs, providing reliable reference value for continuous improvement, optimization, and product quality provision.
Table of contents
- Product Introduction
- Industrial Vacuum Furnace List
- Industrial vacuum furnace advantage
- Industrial vacuum furnace advanced features
- Industrial vacuum furnace Technical Parameter
- Industrial vacuum furnace Manufacturers factory
- The function of each part
- Industrial vacuum furnace Manufacturers
- Industrial vacuum furnace Applications
Industrial Vacuum Furnace List
Industrial vacuum furnace advantage
Temperature uniformity
Independent temperature control in multiple regions to achieve high-precision temperature uniformity, up to ± 1 ℃
Intelligent control system
PLC centrally controls the vacuum furnace, and users can achieve logic command programming control through the touchscreen.
Equipment fault identification
If there is a malfunction during the heat treatment, the Industrial vacuum furnace will immediately sound an alarm and provide suggestions.
Nitrogen gas protection
Some heat treatments need the vacuum furnace to be filled with nitrogen gas, which has this function.
Loading vehicle
It has a special mechanized loading vehicle, and metal parts can be easily removed from the cabin.
Closed water cooling
Water cooling devices and diffusion tubes achieve rapid cooling, improving work efficiency.
Industrial vacuum furnace advanced features
There are 8 thermocouple inputs and multi-channel temperature recorders on the furnace shell to control the uniformity of temperature, with a maximum accuracy of 0.5 ℃
There are multiple layers of 304 stainless steel plates for insulation inside the furnace, with ceramic gaskets in the middle of each layer of stainless steel to isolate it from corrosion by nickel, copper, and other metal elements.
The furnace door has a rotating locking device driven by a cylinder. When the furnace door is closed without locking, the industrial vacuum furnace will issue a warning,
Every component of the vacuum furnace is scientifically designed, and if it is damaged during use, engineers can easily replace it with a spare part.
Industrial vacuum furnace Technical Parameter
Cabin size | 90 * 90 * 120cm |
Max temperature | 1350℃ |
Ultimate vacuum pressure | 1-10 * 5mmHg |
Temperature uniformity | ± 1 ℃ |
Temperature control | 8 zones |
Load capacity | 3 tons |
Touch screen language | English and Chinese |
Power supply | 3-phase 380V |
Vacuum pump brand | China |
Loading vehicle | Including |
Heating efficiency | 500 ℃ per hour |
Cooling method | Water cooling |
Furnace door | Automatic locking |
Industrial vacuum furnace Manufacturers factory
The function of each part
Vacuum furnace body
This is the workspace of the vacuum furnace, where all parts must undergo heat treatment. Each vacuum furnace has a different space size, and users can purchase the appropriate size according to their production needs.
Usually, the furnace body consists of a furnace shell, insulation materials, windows for observing the interior, cooling devices, heating systems, insulation, nitrogen protection, and other components,
The furnace door is a key part, and inert gas is fille into the furnace under a vacuum, which puts higher requirements on the sealing and pressure resistance of the furnace door. Therefore, the design of the furnace door will have an automatic locking device.
The function of vacuum pump
The vacuum unit of industrial vacuum furnaces is composing of multiple vacuum pumps, such as diffusion pumps, Roots pumps, slide valve pumps, and rotary vane pumps, which play an important role in delivering under different vacuum pressures.
When the vacuum furnace is preheated, the rotary vane pump starts working. It is small, lightweight, and has an excellent energy-saving effect in low vacuum environments.
The diffusion pump starts working when high vacuum pressure is desired. It has a strong power output and can quickly reach the ultimate vacuum pressure. This pump is usually install in vacuum furnaces that require high vacuum heat treatment.
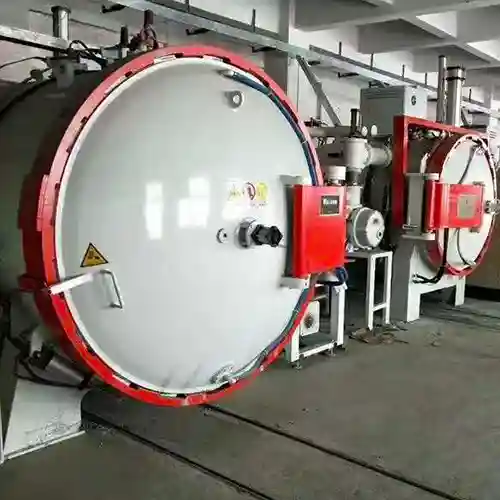
Water cooling device
Every industrial vacuum furnace is with a water cooling device, which serves to absorb the heat generated by the furnace body and maintain a safe temperature range,
Water cooling devices usually consist of water circulation pumps, cooling towers, water-cooled coils, and other parts. The water-cooling coils is install between the compartments of the furnace body,
so strict sealing tests are needs to ensure that the water-cooling tubes do not leak while manufacturing the furnace body.
Another function of the water cooling device is to cool down the vacuum furnace and improve work efficiency quickly.
Industrial vacuum furnace Manufacturers
As China’s top vacuum furnace manufacturer, we produce 35-50 vacuum furnaces annually to provide global users the best vacuum heat treatment solutions. Whether your heat treatment process is quenching, brazing, or sintering, our engineers can provide the best technical support.
For a long time, we have continuously optimized our design, improved the humanized and intelligent operation mode, and solved technical problems in heat treatment for users. Even if you are a new heat treatment engineer, running our vacuum furnace can quickly obtain high-quality products.
Industrial vacuum furnace Applications
Almost all industries require vacuum furnaces to improve product quality and meet special application needs in modern industrial heat treatment production. Let’s give a few examples of the most widely used industries.
- Aluminum brazing
In modern industrial production, some specially structured aluminum parts require multiple parts to be weld. Ordinary welding machines cannot meet this special requirement, so brazing and vacuum furnaces play their roles.
For example, aluminum parts for automobiles, special parts for aerospace, industrial heat exchangers, and other complex structural parts require brazing vacuum furnaces for oxygen-free vacuum welding.
- Quenching and tempering
To fully utilize the performance of metal parts, it is necessary to quench and harden them during the manufacturing process, and a quenching vacuum furnace is the best solution for this process,
- Powder metallurgy
Some powder metallurgy parts need to be sinter in a vacuum environment to ensure the performance and quality of the parts and to avoid oxidation and contamination that can damage the properties of the metal
- .Surface treatment
This heat treatment is a process that improves the surface of metal parts to enhance their durability and wear resistance, usually through carburizing or nitriding.