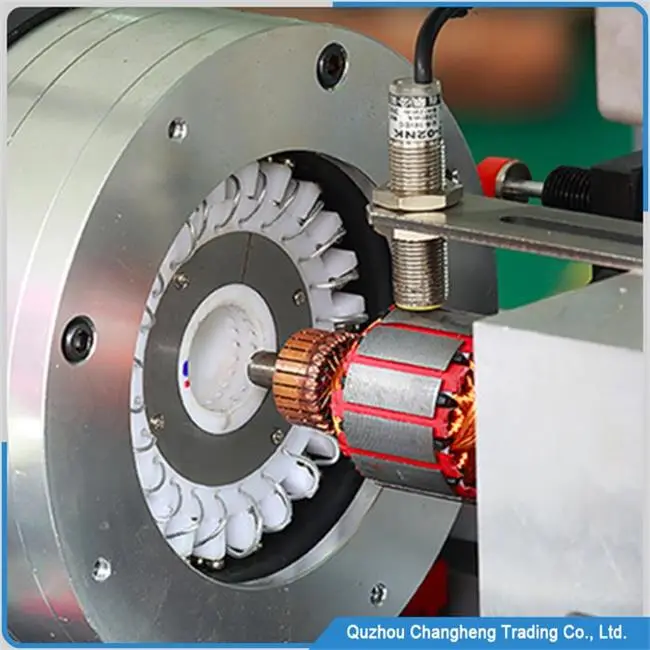
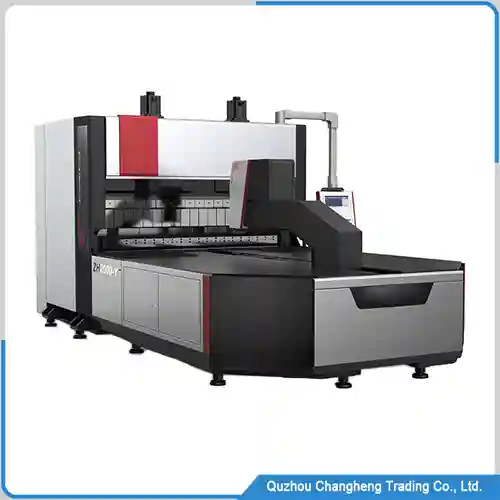
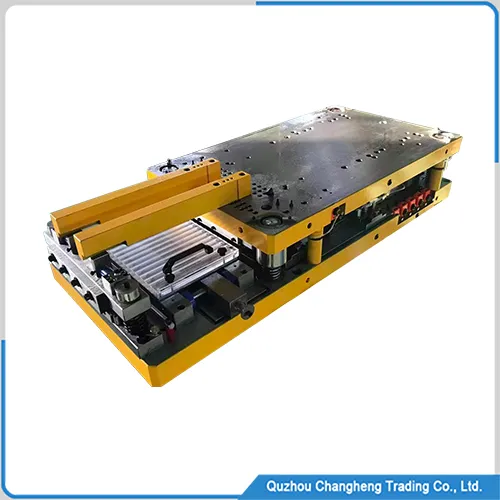
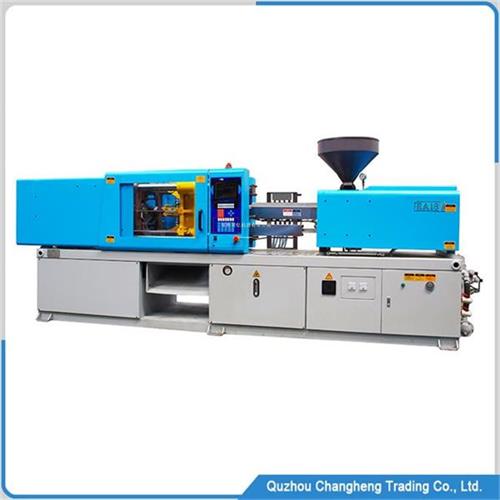
Overview
The motor core stamping die is a tool specifically designed to manufacture motor rotor components. During the stamping process, the metal sheet is formed by high-speed pressing through a stamping die, ultimately forming the required rotor shape and size.
Stamping dies usually include upper and lower molds, which are used together to form the inner and outer contours of the rotor.
The upper die usually contains a stamping convex die, while the lower die contains a stamping concave die.
During the stamping process, the metal sheet is placed between two molds, and then under the pressure of the stamping machine, the sheet is forced to pass through the gap between the upper and lower molds, resulting in plastic deformation and forming the shape of the rotor.
This mold can freely set the height dimension of the rotor according to the thickness of the sheet metal,
which means that one mold can produce motor cores of different heights, and the entire production process does not require worker supervision
Motor core stamping die date
No. | ITEM | DATA |
1 | Motor core size | follow the design |
2 | Core type | laminated |
3 | Mold material | SKD11 |
4 | Production type | continuous pressing |
5 | Mold Usage | Production of Motor Core |
6 | Service life | Press 100 million times |
7 | Mold color | default green |
8 | Rotary drive | servo motor |
motor core stamping die characteristic
1, High efficiency:
This mold is designed for large-scale production and can quickly and continuously produce a large number of identical motor rotors
2, High precision:
Stamping molds can ensure that the size and shape of each rotor meet precise specification requirements, ensuring product consistency and quality.
3, High material utilization rate:
The design of the motor core stamping die can maximize the use of raw materials, reduce waste, and thus lower material costs.
4, High degree of automation:
Stamping molds are usually used in conjunction with automated equipment, such as automated feeding, stamping, and picking mechanisms, reducing manual intervention and labor intensity.
5, Long lifespan of molds:
High-quality mold materials and precise processing technology enable molds to have a longer service life, reducing the frequency of replacement and maintenance.
6, Easy maintenance:
The motor core stamping die is usually designed with structures that are easy to inspect and maintain, making daily maintenance and troubleshooting relatively simple.
Q & A
A: Installing a servo motor on the mold can achieve a rotating iron core, and we have this type of mold
A: Usually 45 days
A: A regular punch press is sufficient, and it is best to choose a fast production punch press.