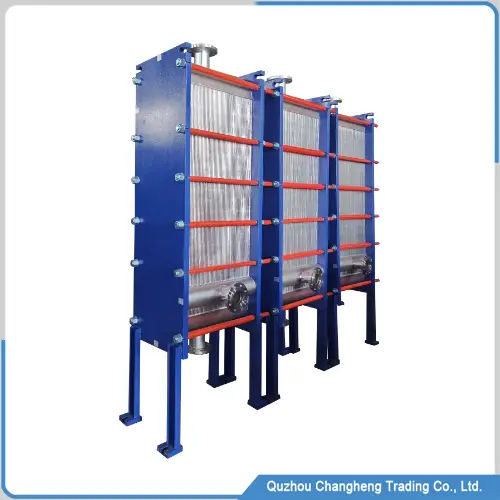
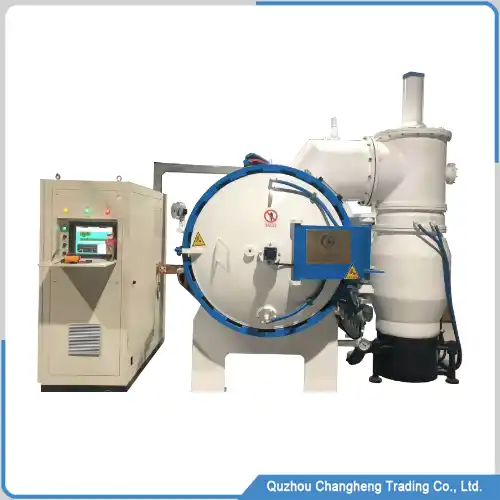
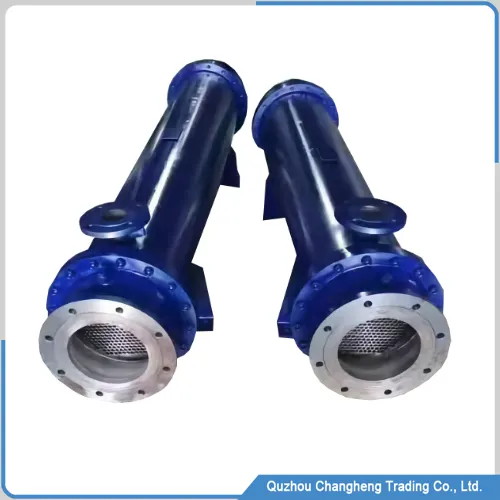
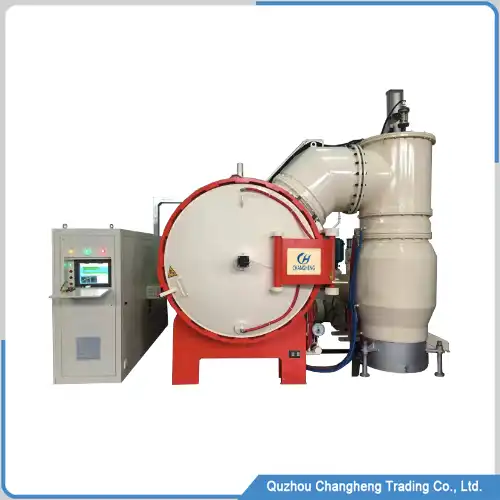
Product Description
The plate to plate heat exchanger is one of the essential coolers in modern industry. It uses advanced corrugated plate stacking technology and a unique flow path structure design. Fluid forms a strong turbulence inside, thus achieving efficient heat exchange. Compared with the traditional tube-and-shell type heat exchanger, the heat exchange efficiency increases by 3-5 times.
Its interior is a 0.5mm ultra-thin stainless steel 304 plate, and its safety can reach food grade. Therefore, this heat exchanger can be safely used in the medical industry, food factories, biological research, and other fields.
Plate to plate heat exchanger special function
Some unique industries, such as petroleum refining, seawater desalination, and the chemical industry, have stricter requirements for heat exchangers. Because the cooling medium in these industries is highly corrosive to metals, these heat exchangers typically use Hastelloy alloy as the raw material for the plates, extending their lifespan.
This type of heat exchanger is designed to be disassembled. When it is used for a long time, there may be some dirt in the corrugated channels, which may reduce the heat exchange efficiency. Users can disassemble it to clean the inside and improve heat exchange efficiency.
Application fields of plate to plate heat exchangers
This heat exchanger is widely useing in modern industrial production due to its high-efficiency heat exchange capability and flexible adaptability. Here are some examples of its usage scenarios:
- Chemical industry:
Plate heat exchangers are essential in chemical production, heating, cooling, condensing, and evaporating. They can efficiently handle corrosive media and meet production requirements.
- Food and Beverage Industry:
In food processing, it is useing for pasteurization, high-temperature sterilization, cooling, and heating to ensure food safety and quality.
- Pharmaceutical industry:
The pharmaceutical industry has exceptionally high-temperature control requirements, and plate heat exchangers can provide precise heat exchange solutions for drug production.
- Energy and Power Industry:
Heat exchangers are used in power plants and renewable energy systems to recover waste heat and incredible processes, helping to reduce energy consumption and operating costs.
Plate to plate heat exchanger Quick details
- Structure: Plate and frame
- Maximum pressure: 1.5mpa
- Ripple design: multi-channel
- Plate materials: stainless steel, titanium alloy, Hastelloy, etc
- Frame material: ordinary carbon steel
- Color: The default is blue
- Minimum order quantity: 1 piece
- Exchange time: About 35 days
- Heat exchange area: Follow the user’s design
- Packaging: Wooden box
- Entry and exit: There are dust covers
Manufacturing process
Plate heat exchangers require precise manufacturing processes. To ensure they do not leak during high-pressure use, the following are the key steps in their manufacturing process:
- Material selection:
The raw materials for key parts are usually high-quality stainless steel, titanium alloy, Hastelloy, or other corrosion-resistant materials to ensure long-term stable operation in harsh environments.
- Sheet forming:
High-precision molds and advanced stamping technology shape metal sheets into a corrugated form. This scientific corrugated channel promotes fluid turbulence, effectively improving heat transfer efficiency.
- Quality Inspection:
Each plate heat exchanger must undergo rigorous quality testing before leaving the factory, such as high-pressure testing, independent channel testing, appearance inspection, size verification, leakage detection, and performance validation to ensure its reliability and safety.
- Manual assembly:
The plates are assembled through stacking and sealing processes to form multiple parallel flow channels. Each channel flows independently without cross-flow, making this design easy to update and maintain.
The advantages of a plate heat exchanger
- Efficient heat transfer: The scientific corrugated layout design significantly increases the heat exchange area, promoting fluid turbulence and improving heat transfer efficiency.
- Compact design: Compared with traditional shell-and-tube heat exchangers, plate heat exchangers are smaller and can be placed horizontally or vertically, taking up less space, which is very suitable for places with limited space.
- Energy-saving and environmentally friendly: Its operating cost is zero during use, and environmental issues such as carbon emissions are not a concern.
- Flexibility and scalability: The modular design makes the plate heat exchanger easy to expand, and its heat exchange capacity can be adjusted simply by increasing or decreasing the number of plates.
- High adaptability: It can handle various fluids, such as seawater, chemicals, petroleum, etc., including high-temperature and corrosive media, to meet diverse production needs.
Plate to plate heat exchanger factory video
Maintenance and repair
Regular maintenance and upkeep are crucial to ensure the heat exchanger’s long-term stable operation. Here are some maintenance steps we recommend:
Regular check:
Regularly check the appearance of the heat exchanger and its components such as valves and fasteners, and replace aging parts in time to prevent leakage and performance degradation.
Cleaning and maintenance:
Dirt and grime can quickly accumulate inside the plate, and if your medium contains sediments, you need to clean the inside regularly to maintain efficient heat exchange performance.
Appearance inspection:
Check the appearance regularly. If the frame becomes rusty, try to remove it and repaint it as soon as possible.
Record and track:
Detail every maintenance procedure to keep track of the heat exchanger’s operating status and predict potential risks.
Conclusion
With their efficient, compact, flexible, and reliable features, plate heat exchangers have become indispensable heat exchange equipment in modern industry. Whether in the chemical, food, pharmaceutical, or energy fields, they can provide excellent solutions to help enterprises improve production efficiency, reduce operating costs, and achieve sustainable development.
Choosing high-quality plate heat exchangers is an investment in equipment and guarantees the company’s future competitiveness.
The plate-to-plate heat exchanger is the ideal solution for an efficient and reliable heat exchange. Let’s work together to propel your business to new heights!