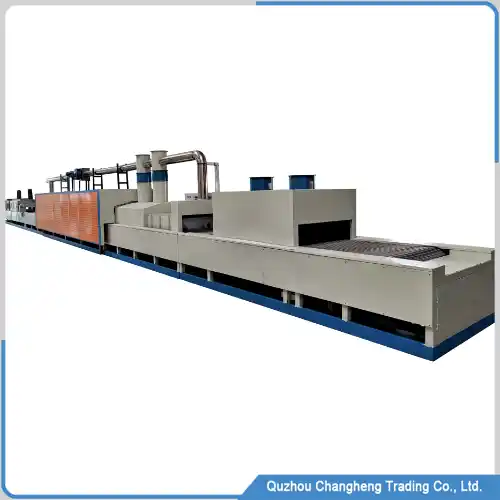
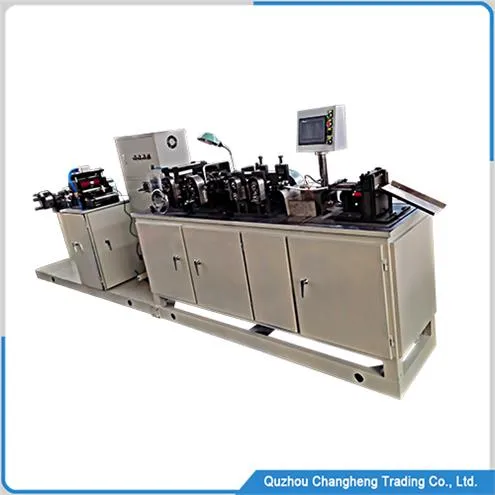
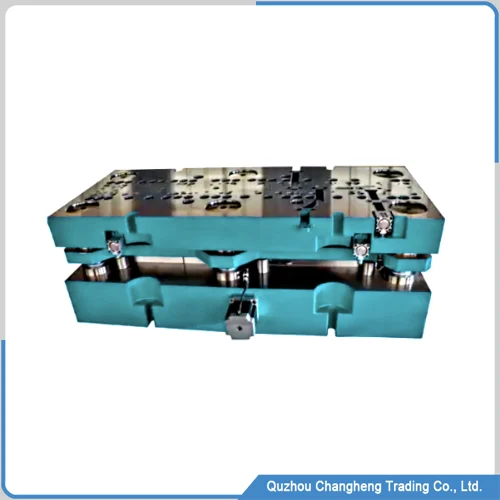
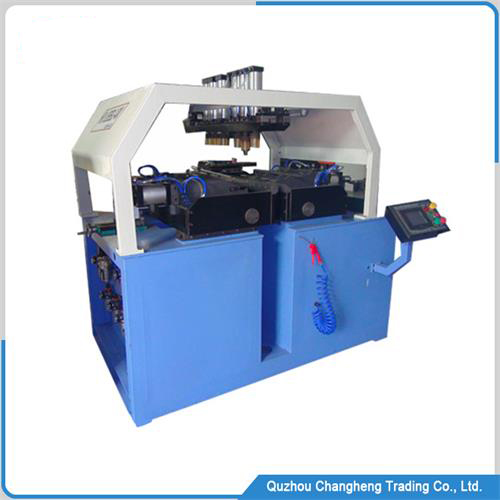
Machine Overview
The radiator tube machine realizes the rapid conversion of aluminum foil materials into radiator tubes through an efficient production process. The machine first presses the aluminum foil into the desired tubular structure through a roll forming process.
Then, the joints of the pipes are welded firmly using high-frequency welding technology to ensure the sealing and structural strength of the pipes.
The welded tubes are again put through a stick forming process to adjust to a precise O-shaped cross-section. Finally, the flying shear device performs chipless cutting to cut the pipe to the set length.
This radiator tube machine is extremely efficient and can produce up to 120 meters of tubes per minute, making it ideal for high-volume production.
Due to its high degree of automation and precise production process, this machine is widely used in the manufacturing of automotive aluminum radiators and other cooler products.
It not only improves production efficiency, but also ensures product consistency and high quality, meeting the strict requirements of modern industry for radiator pipes.
Radiator tube machine data
ITEM | DATA |
Voltage | 168kw |
Production speed | 120m/min |
Power supply | 380/50hz |
Material thickness | 0.28mm |
Cutting off mode | Chipless flying shear |
Welding | High frequency |
Material | 7072/3003 7072/3003/4343 |
Production type | Automatic |
Radiator tube machine production process
The specific production process usually includes the following steps:
1, Aluminum foil preparation,
Select the aluminum foil material of appropriate thickness and install it on the feeder of the machine. The device will automatically convey the aluminum foil through changes in production speed.
2, Stick forming,
The aluminum foil passes through multiple sets of rotating rollers and is squeezed and pulled by the rollers to form the required tubular structure. This process can be one-time molding
3, High frequency welding,
The formed tubes are connected through high-frequency welding technology to form a closed olive-shaped aluminum tube.
4, Roll into shape again,
After welding is complete, the tube may need to be cooled and rolled again to achieve the exact size and shape.
5, Chip-free cutting,
When the tube is completely formed, it is cut to the set length without any chips, and the entire production process is over.
The design of the radiator tube machine makes the entire production process highly automated, thereby improving production efficiency and product consistency.
This kind of machine is suitable for mass production, especially in the manufacturing of automotive aluminum radiators and other cooler products, and can meet the requirements for high strength, high precision and good heat conduction performance of heat pipes.