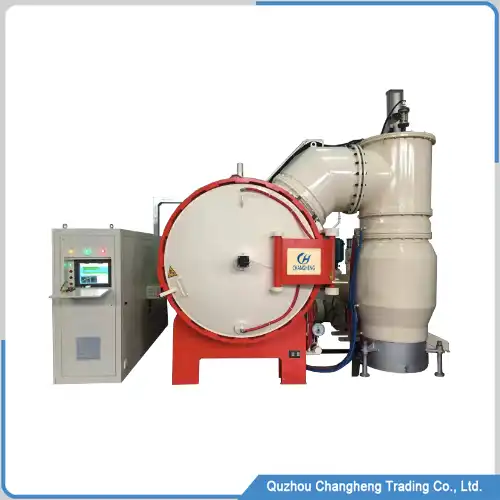
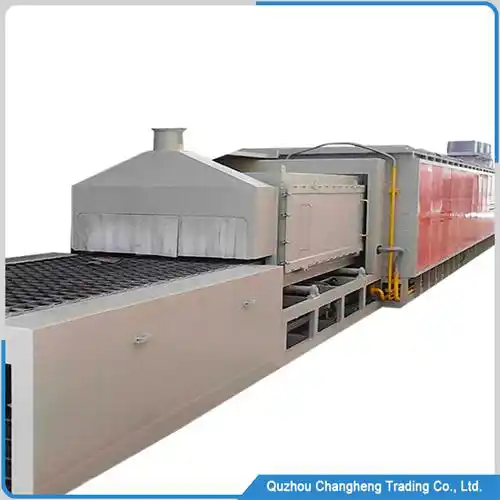
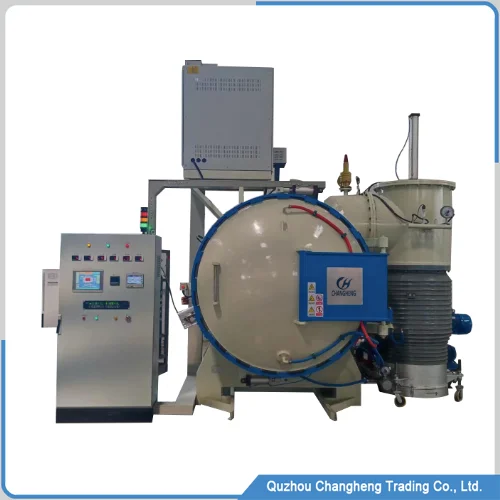
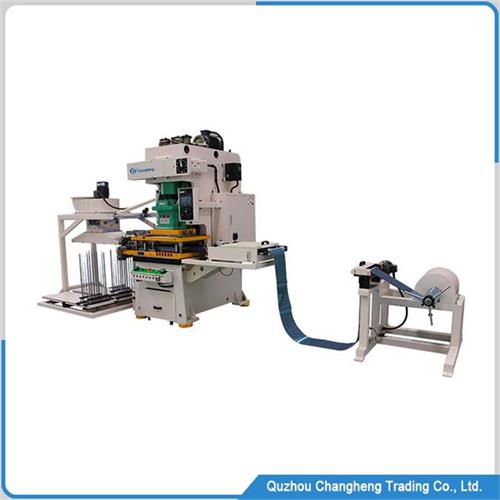
How does vacuum brazing work, A Vacuum brazing furnace is a large Bai-type heat treatment equipment, that can carry out vacuum brazing, vacuum annealing, vacuum aging, and other processing.
Several different programs can be programmed to control and program hundreds of heat treatment curve points, which are divided into six zones: upper, lower, left and right, front and rear. There are multi-point and single-point temperature recorders and over-temperature protection devices.
The furnace temperature uniformity can be controlled within the constant temperature range. In addition, it is equipped with high-purity nitrogen and high-flow forced cooling devices.
The equipment has the advantages of large furnace loading capacity and high efficiency, and no supplementary process is needed for complex parts and parts with special requirements.
vacuum brazing work Purpose:
It is mainly used for vacuum brazing of aluminum products such as aluminum alloy heat exchangers, brazing of stainless steel, titanium alloy,
cemented carbide, high-temperature alloy, non-ferrous metal, vacuum tempering of high-speed steel, tool and die steel, bearing steel, stainless steel, aging and annealing treatment of non-ferrous metal, and vacuum brazing of stainless steel heat exchanger, oil cooler and stainless steel heat preservation cup.
characteristic:
1. The district heater is used to make the temperature uniformity in the heating area consistent.
It can keep the workpiece clean in a vacuum.
Composition:
The vacuum system is mainly composed of the vacuum chamber, pump system, control valves, and heat exchanger. The pump system consists of a mechanical pump, maintenance pump,
roots pump, and diffusion pump. The valve consists of a front stage valve (butterfly valve), bypass valve (butterfly valve),
maintenance pump valve (butterfly valve), and high valve (plate valve). Each valve is a pneumatic valve controlled by a PLC pneumatic valve.
The heating chamber is mainly composed of a stainless steel heating chamber shell, stainless steel reflector, heater, ceramic insulator, water-cooled electrode, furnace bed, etc.
Vacuum brazing work principle
When the vacuum system works, first start the mechanical pump, maintenance pump, and diffusion pump (heating), then open the front valve and maintenance pump valve to vacuum the diffusion pump.
When the vacuum reaches a certain set value of the system, the roots pump is started, the bypass valve is opened, and the front stage valve is closed.
At this time, the vacuum chamber is pumped low. When the diffusion pump is heated to the specified temperature and the vacuum degree is higher than the specified value,
the high valve is opened, the bypass valve is closed and the front valve is opened. At this time, the vacuum chamber is vacuumed to meet the requirements of the process before heat treatment.
After the heat treatment process is completed, the vacuum chamber is filled with high-purity nitrogen by the heat exchanger for forced cooling to complete the whole process.
As for the price, there is a big gap. The configuration differs depending on the size of the effective area you need and the different materials. There will be a lot of difference.
ITEM | DATA |
Temperature | 620 ℃ |
Temperature control | 6 zones |
Heating time | 2.5 hours |
Temperature collection | thermocouple |
Vacuum brazing work process
A vacuum brazing furnace is to clean and decontaminate the parts of the workpiece to be welded with flux, lay the solder, and put another part.
Fix the two parts in the furnace and heat it up to the temperature of the solder to complete the welding. It uses the furnace temperature to raise the temperature of the workpiece,
and melts the solder whose melting temperature is lower than the workpiece so that the workpiece can be welded.
In this process, heating should be as slow as possible to keep the internal and external temperatures of the product to be brazed consistent,
otherwise, the brazing quality will be directly affected. In industrial production, preheating and holding temperature,
energy storage temperature and heat preservation, brazing temperature, heat preservation, and power cut cooling
are effective technological processes that can achieve the above purpose and improve production efficiency. The key factors affecting brazing quality are the vacuum brazing temperature and holding time.